Technology in the service of art
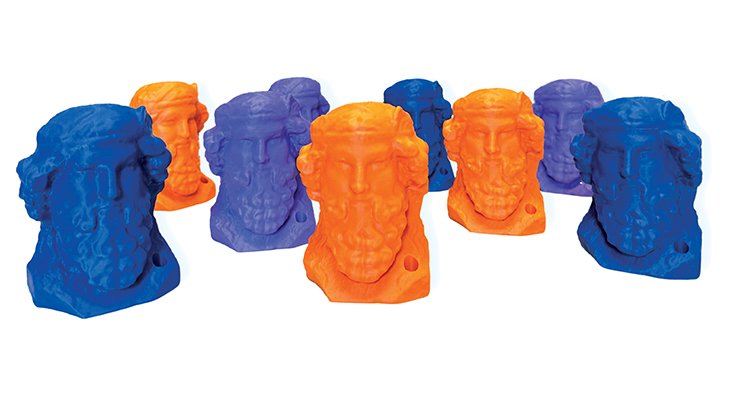
With a nod and a wink to the Paris 2024 Olympic Games and the future materialisation in Songeons Park of the path linking the Musée Antoine- Vivenel and its outsourced temporary exhibition room, the nine 3D-printed so-called ‘hermes’ head-dresses mounted on pillars that two UTC students have created illustrate the long-standing partnership between UTC and the museums of Compiègne.
At the Musée Antoine-Vivenel in Compiègne, you will have to wait until 15 June and the opening of the So Greek! exhibition organised around the museum’s collection of Greek vases (the second largest after that of the Musée du Louvre in Paris) before you can see the installation of nine 3D-coloured copies of the marble Hermes head-dresses that it holds. As part of the 2024 Olympic Games, the exhibition will feature the Panathenaic vases presented to the winners of the ancient Greek Games, several of which are held by the museum. It will also be an opportunity to display the head of Hermes, the original model of those made in 3D to mark out the path linking the Musée Antoine-Vivenel to its temporary exhibition room in the park at Songeons.
These life-size reproductions, mounted on pillars, are the result of work carried out between September and December by Mélissa Rousson-Marchand, a student from Utrecht in TC03, and Swann Courme, enrolled this year in IM01. To address the issues of accessibility and visibility in a site with listed surroundings, to appeal to younger audiences and to dust down our ways of mediation, we took as our starting point the head of Hermes which, in Ancient Greece, was installed on quadrangular pillars to mark out roads, crossroads and the gardens of wealthy houses,» explains Delphine Jeannot, Director of the Museums of Compiègne, who initiated this project commissioned from UTC. It was interesting to pick up on this usage by using bright pop colours. The hermes head-dresses have a very modern, anachronistic feel to them, which is both offbeat and assertive.
A project using an agile evolutionary method
For this project, Mélissa Rousson-Marchand and Swann Courme understood the technical constraints inherent in respecting the work and completing a project using an agile evolutionary method. At the UTC Fablab, the duo developed their technical skills in 3D printing, image capture and STL file conversion. «We chose the methodology and carried out a technology watch focusing on the methods for digitally capturing an object for 3D reconstruction, as well as the most suitable materials,» explains Mélissa Rousson- Marchand. Like the ASA (acrylonitrile styrene acrylate) resistant to climatic conditions, humidity and ultraviolet radiation chosen for printing the nine hermes caps. The duo began by taking two hours of images of the model from every angle in order to reconstruct it. «They rearranged the photos and recovered a cloud of points to reconstitute a volume, which was then post-processed to insert the fixing functions,» explains Nicolas Piton, head of the prototyping platform who accompanied the two students. The base was one of the topics of discussion. «We were very focused on the technical aspects and the attachment system, while the museum had an aesthetic vision. We had to speak the same language so as not to alter the integrity of the work or add elements. Finally, the nine 3D prints of the hermes head-dresses were launched at the UTC’s Fablab, each lasting 40 hours. «Combining art and technology is interesting, concrete and outside the UTC framework», says Mélissa Rousson-Marchand.
For Nicolas Piton, working with the art world is nothing new: «We’ve already worked with the Espace Jean-Legendre, for example. As the Fablab is the UTC’s only prototyping platform, I have a global vision of the projects that I support in terms of teaching, research, industrial development, start-up creation, etc. There are around a hundred projects a year. A connected football table is among the projects currently underway, just as the Fablab is currently working with a local manufacturer in the luxury goods sector.
Partnerships for mutual benefit
The engineering work carried out by the students encourages a professional approach through an interactive project with the outside world. This allows us to ask ourselves the right questions and never forget our objectives, which may be different,» emphasises Emmanuel Doré, a lecturercum- research scientist in Mechanical Engineering who supervised the two Utrecht students. The UTC’s strong presence in the region enables us to position ourselves at events and to highlight possible and virtuous collaborations. Partnerships are the common thread running through the teaching programme as a means of developing both technical and intercultural skills in response to a commission. Art is possible through technological diversion, using the tools, software, resources and methods of the UTC, which provides training in construction methodologies and the geometric modelling of mechanical parts,» explains Emmanuel Doré.
For the museums of Compiègne, located in the same local ecosystem, the influence is mutual. « In the context of the renovation of the Musée Antoine-Vivenel, its ambitions and the limitation of financial costs, the focus on new technologies and the possibilities they offer is important,» continues Delphine Jeannot. Today, we can no longer do without this knowledge. For the general public, it’s also a real attraction. »