Enterprise in the age of Industry 5.0
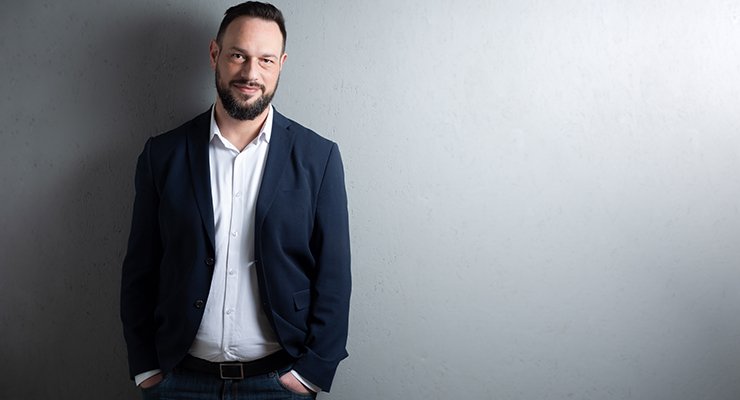
Professor Julien Le Duigou is the titular chair-holder for Mechanical Engineering and a research scientist at UTC’s Roberval laboratory. In particular, he is responsible for the department’s «Integrated Production and Logistics» programme and, I particular, for the “4.0 technologies” course.
Among the course’s aims? «The main objective is to train mechanical engineers with a focus on industrialization, production management and the supply chain, as well as on continuous improvement and implementation of so-called 4.0 technologies. This training provides undergraduates with skills ranging from those used in a methods office which is responsible for defining how to manufacture and industrialize a given product, to actual production in factories and finally distribution of the product to customers», he explains.
First introduced in 2011, the concept of Industry 4.0 concerns the integration of new technologies in the factory. «We’ve been able to inter-connect machines and allowing them to exchange information thereby speeding up decision-making in production. The introduction of new technologies in factories, notably artificial intelligence, augmented reality, the Internet of Things (IoT), digital continuity, the use of Big Data, robotization with Cobots equipped with sensors enabling them to collaborate with an operator, or new production technologies such as metal additive manufacturing, had as its main objective the improvement of the factory’s overall economic performance», he assures.
Industry 5.0
At the time, this was referred to as the 4th industrial revolution, following mechanization, electrification and automation. Today, we speak of Industry 5.0, «more an evolution of the previous phase than a revolution per se. Encouraged and enhanced by the European Union in 2021, this concept aims to redirect the way factories operate. Of course, these technologies will continue to be used, but the emphasis will now concentrate on three aspects. Sustainable development, by using these technologies to facilitate companies’ ecological and energy transition; resilience, or the ability to adapt to hazards such as breakdowns, supply disruptions and market variations, etc.; and lastly, refocusing on the human element, whether in relation to society at large or to the company’s own employees, by putting operators back at the heart of these technologies», explains Julien Le Duigou.
Is there any concrete research work related to this Industry 5.0 theme? «In particular, we are working on optimizing plant production by taking environmental indicators into account. Our work focuses on the impact of a production system, in order to define an optimal mode of operation in terms of energy consumption, for example, and, more generally, environmental or societal impact. The choice of a product’s manufacturing process, the machines on which it will be made and the order in which it will be assembled are all optimized according to cost and lead-time indicators, as well as environmental and societal indicators. We are also working on the theme of the circular economy. In our case, this means helping companies to recycle or even reuse, as far as possible, the parts of end-oflife products by helping them to disassemble them. This is called “Remanufacturing”, and involves recreating new products from old ones. We also work on product quality: how to improve it so as to minimize scrap, rejects and so on. To this end, we use computer vision to detect defects in product appearance using machine learning. Finally, we are working on predictive maintenance, which involves detecting the probability of a machine failure before it happens», he describes.
Genuine interest shown by manufacturers
These are themes which, quite naturally, are of interest to a number of manufacturers. «We work with production line manufacturers such as ALFI Technologies, software publishers such as PTC and manufacturers such as Renault and Safran,» he adds.
But it’s not just the large companies who are affected by Industry 5.0. SMEs and ETIs are also impacted by new technologies. «For example, we have a future industry platform project entitled «Quatrium» with the Centre Technique des Industries Mécaniques (CETIM). Its aim? To be able to help SMEs and ETIs in the Hauts de France region to accelerate their ecological, energy and digital transition. In this project, the aim is first and foremost to popularize these concepts among companies and then to take action to help them assimilate the various technological building blocks. Hence the development of a platform, part of which is located at UTC, enabling them to see the technologies operating in situ and to test them in real life», concludes Julien Le Duigou.
MSD