Des chercheurs investis
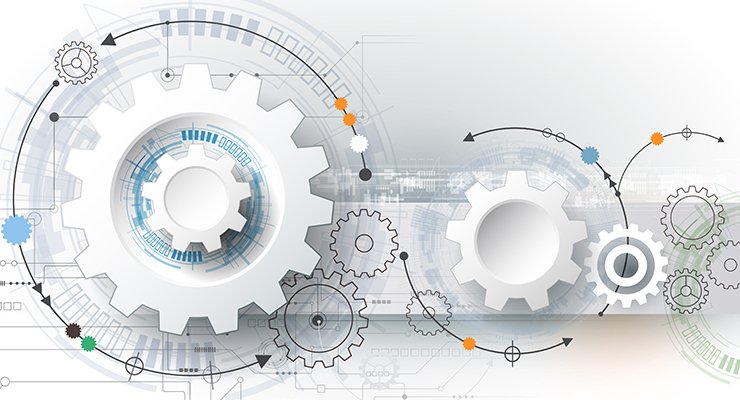
Partenaires de longue date, le centre de recherche ArcelorMittal Global R&D de Montataire, spécialisé dans les applications automobiles, et l’UTC ont créé en 2019 ce laboratoire commun soutenu par la Région Hauts-de-France et en partie financé par le FEDER. Les travaux menés dans le cadre de FuseMetal s’articulent autour du soudage des aciers de haute résistante de troisième génération et de la modélisation des procédés de fabrication additive. Les six doctorants, Elise, Daoming, Héléna, Marcia, Ghassen et Ana Julia présentent leurs travaux de recherche au sein du laboratoire.
Ghassen Dali, doctorant de 3e année, mène une thèse sur la modélisation et la simulation de la fabrication additive métallique pour l’optimisation de la métallurgie et des procédés.
« Le projet de ma thèse a débuté le premier octobre 2020, il s’inscrit dans la stratégie du laboratoire pour développer et renforcer ses compétences sur le thème de la fabrication additive (impression 3D) qui constitue un axe du laboratoire commun FuseMetal. En effet, cette technologie présente un potentiel prometteur car elle permet de réaliser des géométries complexes et non traditionnelles permettant de contourner les contraintes de conception/fabrication imposées par les procédés classiques, de raccourcir les cycles de développement et de réduire les coûts. En revanche, les procédés de fabrication additive peuvent engendrer, lors et après la fabrication, des défauts (instabilité du bain liquide, porosités, des délaminages entre couches, propriétés hétérogènes). Pour remédier à ces inconvénients, l’utilisation de logiciels de simulation est recommandée afin de réduire le nombre d’essais nécessaires à la réalisation d’une pièce conforme aux spécifications techniques en impression 3D). Je travaille donc sur la simulation et la modélisation de l’impression 3D des aciers. L’objectif est de développer des modèles numériques dits prédictifs. Le modèle va être capable de mieux décrire les relations entre les paramètres opératoires, les propriétés de la matière et l’état de fabrication de la pièce finale. »
Marcia Meireles, doctorante de 3e année, mène une thèse sur l’identification expérimentale des liens entre paramètres de procédé, cycles thermiques et transformations métallurgiques lors de la fabrication additive des aciers.
« Mes travaux de thèse portent sur l’étude d’un procédé de fabrication additive de pièces (impression 3D). Cela consiste à fabriquer des pièces 3D à partir de l’ajout de couches successives de matière fondue. Ce procédé étant très prometteur dans le milieu industriel car il permet de fabriquer des pièces avec des géométries très complexes, tout en évitant des phases additionnelles d’assemblage et avec très peu de déchet. Ainsi, l’impression 3D est un procédé qui réunit des capacités remarquables et uniques. Le matériau que j’étudie est un type d’acier développé par ArcelorMittal spécialement pour l’impression 3D. En effet, pour obtenir des pièces qui répondent aux exigences de leur application, il est primordial de bien comprendre l’effet des paramètres d’impression choisis sur la qualité de pièces. C’est pourquoi, dans ma thèse, j’étudie les phénomènes physiques qui ont lieu lors de l’impression 3D et j’évalue leurs effets sur les caractéristiques finales des pièces. Ainsi, le but de mes études est de pouvoir fabriquer des pièces 3D d’une façon optimale. »
Daoming Yu, doctorant de 3e année, mène sa thèse sur l’optimisation des outils d’emboutissage à chaud imprimés en 3D.
« Mon projet de recherche porte sur l’optimisation topologique des outils d’emboutissage à chaud obtenus par la fabrication additive métallique. L’emboutissage à chaud est un procédé de mise en forme dans lequel une tôle est d’abord chauffée dans un four à une température d’environ 900°C. La tôle est ensuite mise en forme à haute température dans une presse et, grâce à un refroidissement intense (au contact des outils froids), des transformations métallurgiques permettent à la pièce finale de présenter des caractéristiques mécaniques élevées (la pièce finale est trempée). Grâce aux hautes propriétés mécaniques ainsi obtenues, il est possible de réduire les épaisseurs des pièces ce qui permet d’alléger les véhicules. In fine, la consommation de carburant et les émissions de CO2 seront réduites. De plus, ce procédé présente plusieurs autres avantages : il permet de former des géométries complexes, nécessite moins de pression de presse, les pièces ne présentent pas de retour élastique, etc. En raison de ces avantages, l’emboutissage à chaud est un procédé de mise en forme largement utilisé pour fabriquer des pièces automobiles. Dans le procédé d’emboutissage à chaud, l’outil est particulièrement complexe, car il intègre un circuit de refroidissement. Il nous a semblé important d’évaluer les potentiels de la fabrication additive pour réaliser ces outils d’emboutissage. Cette technique peut en particulier permettre d’optimiser le circuit de refroidissement et donc d’améliorer l’efficacité du procédé d’emboutissage à chaud. L’objectif est de développer une procédure unifiée de conception des gammes de mise en forme, incluant la conception des outillages en combinant la modélisation du procédé de mise en forme et l’optimisation topologique, en s’affranchissant des contraintes imposées par l’usinage et en tenant compte des contraintes qu’imposent la fabrication additive. Cette procédure est testée sur des prototypes d’outils pour valider la viabilité des solutions proposées en termes de conformité et de tenue des outillages.»
Elise Champolivier, doctorante de 2e année, mène une thèse avec des études expérimentale et numérique sur la modélisation et la transition d’échelles pour la prédiction de la mise en forme de structures assemblées par laser.
« Depuis plusieurs années, les constructeurs automobiles sont constamment mis au défi de réduire la consommation de leurs véhicules tout en conservant leurs performances en termes de sécurité. ArcelorMittal développe de nouvelles solutions pour répondre à ces objectifs en combinant deux technologies : les Flans Raboutés Laser et les aciers à très haute résistance de 3ème génération. La technologie des Flans Raboutés Laser consiste à assembler bout à bout par soudage laser des tôles d’acier de nuances, d’épaisseurs ou de revêtements différents. Les tôles assemblées sont ensuite mises en forme pour obtenir la forme de la pièce automobile : c’est l’étape d’emboutissage. Couplée à l’emploi des aciers à très haute résistance, cette technologie permet à performances égales d’alléger les pièces automobiles tout en conservant les propriétés de résistance. Ma thèse porte sur l’étude de la formabilité des Flans Raboutés Laser constitués d’aciers de 3ème génération. Mon travail consiste à étudier le comportement mécanique des soudures de ces assemblages lors de l’étape de mise en forme pour définir des recommandations et des critères de rupture que les industriels pourront appliquer pour concevoir leurs pièces. L’étude se base sur des expériences qui permettent d’alimenter des modèles numériques dans le but de développer des modèles de prévision du comportement des assemblages soudés laser. »
Ana Julia Vasconcelos de Moreira, doctorante 3e année, mène une thèse sur l’évolution de microstructures locales des aciers de 3e génération en présence de forts gradients thermiques et chimiques.
« Ma thèse porte sur l’étude des assemblages de deux tôles d’acier de 3ème génération, identiques ou différentes, par soudage laser pour la fabrication de pièces automobiles Afin de répondre aux exigences de l’industrie automobile concernant la réduction de poids et l’amélioration des performances mécaniques. En plus de répondre à ces exigences, la technologie du soudage laser permet de concevoir des pièces automobiles ayant des propriétés spécifiques là où elles sont nécessaires. Le défi réside dans le changement des caractéristiques et du comportement des aciers autour du cordon de soudure, en raison des hautes températures atteintes lors du soudage laser suivies d’un refroidissement rapide. Par conséquent, j’étudie les différentes zones des différents assemblages d’aciers conçus par ArcelorMittal, afin d’identifier et de comprendre l’origine des défauts mécaniques et métallurgiques et ainsi pouvoir optimiser le processus de soudage au laser. »